RevoTech recycling technologies from Bandera are systems for the up-cycling of post-consumer Polyolefins and PET which meet the demands of food packaging regulations.
Polyolefins Recycling
Bandera manufacture RevoTECH recycling lines using their highly developed twin screw technology, for the processing of post-industrial or post-consumer scrap. They offer customised solutions for all grades of polypropylene and polyethylene.
Two configurations are available:
Co-Rotating Single Twin Screw Extruder
- Good for all polyolefins (not the case with single screw extruders)
- For processing of well selected and pre-washed feedstock
- High levels of degassing and super filtration system (mechanical decomtamination)
- Extended vacuum zone – 52 L/D ration co-rotating screws with low shear design
- Good mixing for high level of homogenisation and energy efficient compounding
- Under-water pelletising system
- Can produce finished material for injection or blow moulding operations
Cascade System
Two twin screw extruders (the out-feed of the first, feeding to the second). A more comprehensive process for producing a higher quality product.
- The mot efficient system for up-cycling – gives a high grade technical solutions for low grade material
- Can process very dirty feedstock with two or three stage filtration. Increased levels of filtration can also be specified if required.
- Two de-gassing stages to reduce VOC (volatile organic compounds, often referred to as volatiles) and odours
- The second extruder allows the addition of virgin polymer and/or additives for modification and balance of the melt (MFI) – for the production of either raw material or pellets
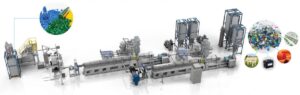
- Melt flow index measurement system for controlled adjustment and repeatabillity
- Fast colour change – due to self cleaning capability of the screws
- De-odourising system available for increased odour extraction
- Processed pellets can be sold as “Second Use Virgin Material”
Polyester Recycling
Bandera has a very long history of manufacturing extrusion lines for processing PET film and sheet for the food packaging sector and that extrusion technology, together with the expertise gained in minimising degradation and maximising purification, has been hugely beneficial for the development of recycling lines.
HVTSE – Highly Vented Twin Screw Extruders
- Powerful melt venting purification
- Large surface for de-gassing
- Suitable for 100% regrind material
- Low shear stress and low energy process
- Unique ‘dry-less’ technology – absolutely no drying required for PET
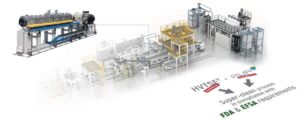
PURe – for PET Food Grade Rigid Film
- Solid state de-contamination system for post consumer PET material – both FDA and EFSA approved
- Can use 100% regrind material for food packaging applications – complying with FDA and EFSA cleaning efficiency requirements
- Can be supplied as a stand alone system, for use with existing lines
- Long lasting components for cost effective maintenance, is proven to run continuously for long periods without having to chaneg components.
- Best IV drop in the extrusion market
- Very low energy consumption
- Effective deodorisation is another benefit of the PURe system.
Bottle to Bottle 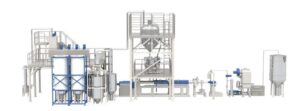
- Bottle flake re-processing by using a combination of the HTVSE and PURe technologies
- Super clean PET pellets produced, ready for the production of new bottles
Tray to Tray
- Bandera have developed an extrusion coating process to enable the re-use of reclaimed PET trays – to form new trays, including those destined for sealable food packaging
- Two coatings are applied to a mono PET substraight, the first giving a barrier layer and the second coating gives the sealing properties required with the top lid film

- The resultant film is equivalent to the multi-material films currently on the market – but now is fully recyclable because only PET is used. (not mixed with other polymers, which can lead to chemical contamination). It also has much better transparency
- This now allows flake from the recycling process to be re-extruded and coated for the production of new trays