Plastic Waste has been significantly reduced by a global leader in the supply of blown fibre cable and ducted network solutions with the use of the Plasmac Omega
Emtelle is a worldwide manufacturer of pre-connectorised, blown fibre cable and ducted network solutions. As part of its four point sustainability strategy, Emtelle has a vision to reduce emissions, improve resource sustainability, reduce plastic waste, and be a fair employer and partner.
One of the components they manufacture for their range of solutions is polyethylene Microducta & sheathed Microduct Bundles for fibre optic cables. In a step to address their desire to reduce plastic waste, Emtelle discussed with UK Extrusion the recycling of scrap tubing & sheathing. They were at that time putting scrap out to a third party for recycling, but could see the benefits of keeping as much of this activity in-house as possible. Continue reading →
What do you do when you have an essential PET Foil & Sheet Line for food packaging, manufactured in Italy, ready and waiting to be shipped and installed in the UK when a worldwide pandemic hits?
Panic, would be an option. However, not in this case due to two secret weapons in UK Extrusion’s customer satisfaction toolbox. Read on to discover what they were and how they convinced the judges of the Plastics Industry Awards to honour an extrusion application in the category of Supplier Partnership – Prime Machinery, for the first time. Continue reading →
Post-industrial waste recycling lines, blown film and sheet extrusion supplier, UK Extrusion, has been delighted with both the attendance at Interplas UK and with the level of enquiries received during the three days of the show and in subsequent days.
UK Extrusion’s debut Interplas UK September 2021 was certainly a baptism of fire. Not just all the usual anxieties for first-time exhibitors, but unique issues surrounding the pandemic and associated concerns. Continue reading →
Plasmac has released their newest variant of the highly successful ALPHA range of direct extrusion recycling systems for the recycling of inline trim.
The ALPHA XS is a very compact, energy-efficient, and highly cost-effective addition to the Alpha range of extruders.
Featuring a reduced footprint of less than 1 sq metre and power consumption of less than 0.2kW/Kg the ALPHA XS also offers the option of a roll feed unit for off-spec reels. Providing output up to 50 Kg/h. this is a magnificent little workhorse.
Plasmac has designed the ALPHA XS with a new air-cooled pelletising system that has increased the cooling capacity by over 50% and the new design of cutting system allows users to set up and forget it.
With a new improved cutting blade with a longer life and better pellet cutting, Plasmac believes the Alpha XS will set the standards for inline recycling systems for in-house industrial waste recycling.
When a global leader in the design and manufacture of extrusion lines for plastic packaging and converting virtually opens its doors to the industry, it’s bound to be a popular event.
Bandera’s Plastic Week 2021 Virtual Open House was held 21, 22, 23, and 25 June hosted by the Bandera Technical Centre, The House Of Extrusion® which specialises in Bandera’s Testing and Research and Development activities. Throughout the week a common theme of the Circular Economy was the underlying trend as Bandera showed their innovation.
Bandera are no strangers to the concept of video streaming from their premises, having been pioneers of the concept during the early days of the pandemic. Their streaming from Italy to the rest of the world, last year, was met with enthusiastic accolades from the plastics industry. Continue reading →
Plasmac has added a new range of Post-Industrial Plastic Scrap Reclamation machinery to its portfolio of effective, energy-efficient recycling machines for post-industrial plastic waste.
The Epsilon range is based around a dual-diameter screw and direct shredder feeding system. A single shaft shredder is mounted on top of the hopper entry. The shredder is cantilevered for easy access to the screw and for cleaning. The shredder is particularly useful for pre-size reduction of some types of feedstock, such as rigid polymers, skeletal waste, thicker trims, and film off-cuts and cut-outs.
At the smaller end of the range, the Epsilon machines are perfect to be used as high-speed inline trim recycling machines or for thicker trims.
The larger Epsilon machines are ideal for the recycling of start-up scrap, injection moulding scrap, and for the recycling of non-wovens.
Depending on the application, Plasmac offers two types of pelletising systems, either AIRCOOL or HYDROCOOL. Normally, the smaller machines would be AIRCOOL and the larger machines can be supplied either AIRCOOL OR HYDROCOOL.
There are a number of standard options available to ensure that this system is perfect for your needs and our team are happy to discuss these with you.
Bandera will host a Live Streamed Open House from their House of Extrusion facility near Milan on May 12th & 13th 2020
Participants will have the opportunity to see a Bandera complete 5-layer co-extrusion blown film line for HDB (Heavy Duty Bags) and FFS (Form, Fill, Seal) applications.
The HDB Flex lines offer excellent results for features required by processors such as weldability, processability and printability. As processors require minimised film thickness the company has taken on this challenge to meet its customer’s requirements.
In collaboration with Borouge, a manufacturer of polyolefins and Frilvam Masterbatches, Bandera will be showcasing the latest innovations. Bandera are worldwide specialists in the design and manufacture of Blown Film Lines and a globally recognised brand in the plastics industry. This will, therefore, be an excellent opportunity to view one of their technologically impressive lines in comfort.
If you would like to discover more about our Blown Film Lines visit our dedicated page to download some basic information.
The event will be available for three sessions over the two days enabling participants to take part whatever their schedule.
Click here to register for your choice of day and time.
Multi-layer rigid film lines operating at the Bandera House of Extrusion until December 17th 2019. These lines are designed to enhance the use of recycled/bio compostable materials within the circular economy.
- PET/PLA Multi-layer Rigid Film Line (with organic barrier material) up to 5 layers
- PET/Foam PET/PP Multi-layer Rigid Film Line (with high mineral filler percentages) up to 5 layers
- Condor Line PET/PP/PLA/PS/Foam Technology Multi-layer Rigid Film Line (with inline extrusion coating unit) up to 11 layers
- PO/EVA Waterproof geomembrane 2-layer Flat Die Line
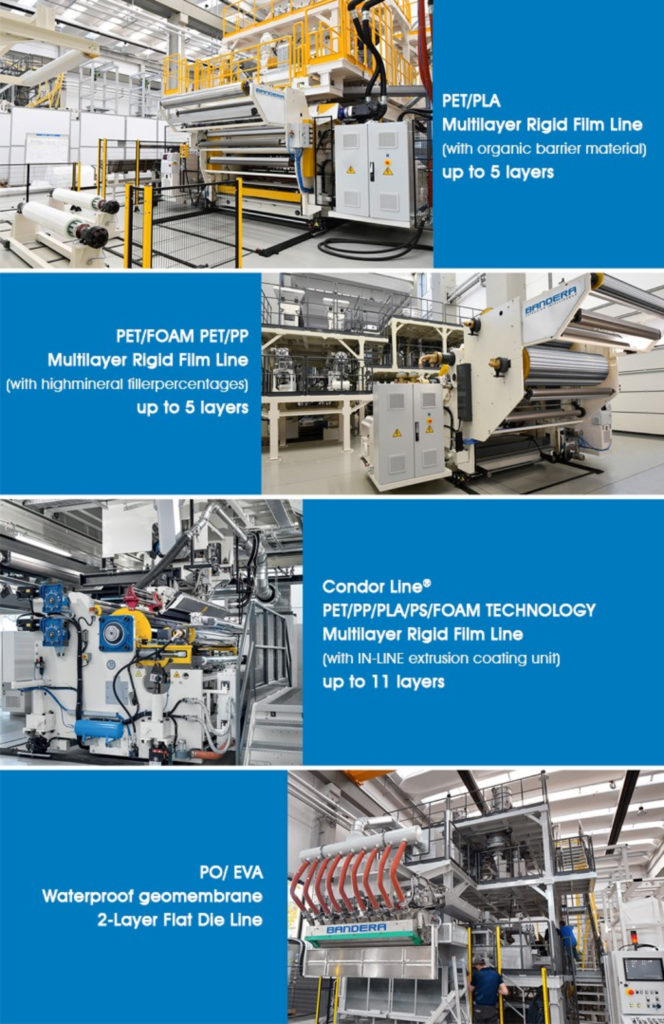
Bandera, designers and manufacturers of complete extrusion lines for packaging and converting are increasing the possibilities for visitors to K2019.
In addition to exhibiting a working 7-layer barrier and high barrier film line in Hall 17, Stand C07 at the Dusseldorf show, Bandera are offering the unique opportunity to visit their Research and Development Centre in Busto Arsizio. The centre is conveniently placed close to Milan’s Malpensa Airport, which is 1 hour’s flight time from Dusseldorf.
Continue reading →
A 7-layer, complete co-extrusion Blown Film line will be presented by Italian manufacturer Bandera at K2019, October 16 – 23
The Barrier Flex® Seven is a fresh concept in the Bandera 7-layer co-extrusion Blown Film line series and will be in operation in Hall 17 Stand CO7.
Combining barrier and high barrier film, the Barrier Flex® Seven is an optimised co-extrusion line which offers customers short run, fast production changes and high-throughput polyolefin film production with a ground-breaking core. Continue reading →